Machine Setup POWER Parameters
Initial Units are: G20 Inch or G21 Metric to power up in inch or metric.
Number of Axes: Can be 1 to 5.
Power-On Feedrate: Can be any number up to the maximum feedrate.
Spindle Axis: 1 to 5 1=X, 2=Y, 3=Z, 4=A, etc. Normally set to 3 for Z axis.
Primary HDW Encoder Axis:
The encoder to use for the primary handwheel. 8 for CNC8000 systems.
2nd Handwheel: Used for optional dual handwheel systems
(4 if it Encoder Axis: has the option).
3rd Handwheel: Used for optional dual handwheel systems
(5 if it Encoder Axis: has the option).
Remote HDW FOV1 thru FOV4: Sets the feedrate for the four feedrate switch
positions on the remote handwheel.
Remote HDW Encoder: The encoder to use for the remote handwheel.
Block Skip On: If Yes block skip is on at power up.
Optional Stop On: If Yes optional stop is on at power up.
Safe Zone On: If Yes safe zone is on at power up.
G22 turns the safe zone off.
G23 turns the safe zone on.
Manual Crank: Set to yes for machines that can be used as manual machines.
Allows X and Y axes to be moved using manual cranks.
Foreign Extension: Refers to the extension for data files. Current valid extensions
are listed below.
NOTE: Shift - F8 will toggle between English and any other language.
CHN CHINESE
ENG ENGLISH
SPN SPANISH
GRM GERMAN
Tool Table by: Radius or Diameter
***** Tool Table Fields *****
The following tool characteristics may be displayed in the tool table.
Diameter⁄Radius type
1. Compensation and Actual sizes. (selects both) For programs that have been compensated
for by CAD⁄CAM systems.The Compensation size is the difference between the CAD⁄CAM
comp size and actual size. The actual size is the physical tool size
-or-
2. Standard. The compensation size and the physical size are the same.
Tool Length: Yes⁄No
Diam⁄Radi Wear: Yes⁄No
Length Wear: Yes⁄No
Load Limit: (used for tool load monitoring) Yes⁄No
High Load: (used for tool load monitoring) Yes⁄No
Max RPM: Yes⁄No
Tool Type: Yes⁄No
****Tool Changer Information****
ATC Type is: Milltronics or Manual
Carousel Side Index Button: Yes for machines with tool loading station
Milltronics ATC is: Plunger, Geneva Two Step, Geneva One Step, Swing Arm,
or HM20 Swing Arm.
ATC tool (pocket count): Number of ATC pockets.
M6 (Tool Change) Macro: Name of the program used for custom M6, for example
“FAST.ATC”
Pot down on swing arm tool: Yes means the pot will be down for the pending
changers: tool. No means it will be up.
Dual-Acting Pot Down On Switch: For ATC’s that have outputs for potup and potdown
Check drawbar unclamped switch: Yes for machines with a proximity switch to detect the
drawbar unclamped.
Check drawbar clamped switch: Yes for machines with a proximity switch to detect the
drawbar clamped.
Drawbar Delay: Generally zero.
The parameter is retained for legacy carousel-style toolchangers as a delay (in seconds)
after the drawbar comes on and before the head goes up.
Arm Style Tool Spacing: The largest diameter tool (in inches) that can be loaded in a
tool carousel without interfering with the neighboring tool. Generally 3.00 Inch ⁄ 75 mm
Custom G⁄M Code Tables
Custom Gcode 09010
Custom Gcode 09011
Custom Gcode 09012
Custom Gcode 09013
Custom Gcode 09014
Custom Gcode 09015
Custom Gcode 09016
Custom Gcode 09017
Custom Gcode 09018
Custom Gcode 09019 |
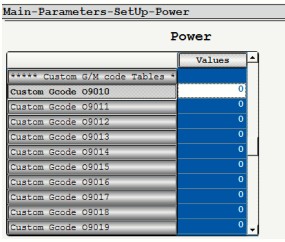
|
Custom Mcode 09020
Custom Mcode 09021
Custom Mcode 09022
Custom Mcode 09023
Custom Mcode 09024
Custom Mcode 09025
Custom Mcode 09026
Custom Mcode 09027
Custom Mcode 09028
Custom Mcode 09029
Custom Mcode 09030
Custom Mcode 09031
Custom Mcode 09032
Custom Mcode 09033
Custom Mcode 09034
Custom Mcode 09035
Custom Mcode 09036
Custom Mcode 09037
Custom Mcode 09038
Custom Mcode 09039 |
When the G or M code is executed the 090## program (in
the ram folder) associated will be called. All custom codes
are checked for syntax errors prior to running any program
(or MDI command). If an error is found (or the 090## file
is not found) a message is shown:
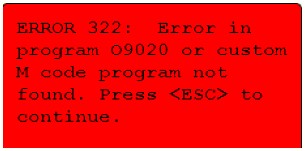
ERROR 322: Fehler in Programm O9020 oder Custom
M Code Program nicht gefunden. Drücke < ESC > für weiter
|
Parameter File Version Used to track software during updates.
*****Inch Precision***** Used for displaying inch values other than axis positions.
Cartesian Leading
Cartesian Trailing
Angular Leading
Angular Trailing
Spindle Leading
Spindle Trailing
Feedrate Leading
Feedrate Trailing
*****Metric Precision***** Used for displaying metric values other than axis positions.
Cartesian Leading
Cartesian Trailing
Angular Leading
Angular Trailing
Spindle Leading
Spindle Trailing
Feedrate Leading
Feedrate Trailing
Notes on Parameters
Note 1: On any given parameter screen, parameter values are written when Escaping to
the main menu. After editing parameters, whether they be Power parameters or any other
parameters, remember to Escape to the main menu before powering down the control.
Note 2: For new power parameters to take effect, the machine must be powered down then
up again. Power parameters are so named because they are read only on power-up.
When the G or M code is executed the 090## program (in the ram folder) associated will
be called. All custom codes are checked for syntax errors prior to running any program
(or MDI command). If an error is found (or the 090## file is not found) a message is shown: